Green Guide: Going Uber Green
04 Jul 2009
If you’re looking to green your home from the ground up, here’s some advice an recommendations from a couple who did just that.
Photos by Ruthanne Johnson The average American home is far from friendly when it comes to the environment. From the petroleum-based roof overhead to the chemically sealed foundation below, the conventional home is an energy hog and chemical reservoir.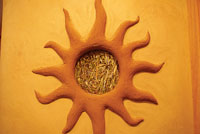
Toasty Home and a Pizza Pie
The masonry heater the Feldmans installed in their home has long been used in northern Europe, where winters are extreme. Also known as a Russian or Finnish stove, this heating system is basically a wood stove encased in stone. The stove burns intensely hot, and the surrounding stones absorb and retain the heat, then radiate the warmth long after the fire goes out. Because the fire burns so hot, it emits a trifling amount of particulates into the air.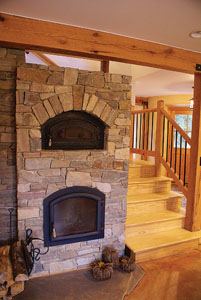
Down the Chute
For their waste-management system—aka the toilet—the Feldmans installed a composting system from Montana-based Advanced Composting Systems. Each gravity-flush toilet on separate floors had to be in close horizontal proximity to the others—3-by-5 horizontal square feet, to be exact—so they could feed into the chute that empties into the company’s Phoenix composter in the basement below. In the style of an old-fashioned outhouse, each toilet has a 12-inch diameter pipe that extends straight down into a two-chamber composting unit constructed from leakproof and corrosion-resistant foamed polyethylene. The top and bottom chambers are filled with wood shavings to facilitate the composting process, and a screened baffle between the chambers separates liquid from solid waste. The top chamber holds the solid waste, while liquid leaches through the wood shavings into the chamber below. A continuously running, 5-watt fan—the system’s only electrical load—keeps air flowing and prevents odors from wafting up into the house. It also helps with evaporation. The manufacturer says the odorless, waterless system is also frost-proof, chemical-free and clog-proof. Jeff says he has to drain some liquid from the system’s bottom chamber every one to two weeks, and turn the compost about once a week, which takes about 30 seconds. He sprays the drained liquid over the top of the compost pile and/or drains some off into a bucket to fertilize the garden. Draining the liquid takes about 10 minutes, tops, Jeff says—about the same amount of time it takes to clean a toilet bowl, which you don’t have to do with the composting toilet because there is no bowl, although visually the exterior resembles a conventional toilet. The chute is a nonstick plastic which material readily flakes off of, Jeff says. But he cautions that toilet lids should remain closed when not in use to keep pets safe. The composting system in the Feldman home accommodates a family of four and only has to be emptied about once every five years. The waste—which has a crumbly texture and smells somewhat earthy after composting—can be used as fertilizer, although it’s not recommended on root crops. “The Phoenix is a very simple system, with no mechanical bells and whistles,” Jeff says, “but it does its job well.”Paper Subfloors
Instead of traditional plywood subfloors, the Feldmans selected a subfloor material manufactured from 98 percent post-consumer recycled paper called Homasote. It was a natural choice, he says, considering plywood layers are bonded with adhesives that outgas carcinogens like formaldehyde. The process used to create Homasote—similar in composition to highly compacted, super-dense papier mâché—minimizes outgassing, and the material is also great for applications where soundproofing is important. The product’s recycled paper keeps trees from being felled and also lessens the amount of trash in landfills. “The nice thing about Homasote is that you can take the scraps, all those little cutoff pieces, to the recycling center,” Jeff says, where they’re wetted down and run through a grinder. But there are downsides to Homasote. “It costs about twice as much as plywood and is much heavier, about 100 pounds for a 4-by-8 sheet,” Jeff says. This was an issue for their construction workers, who had to lug the material up to the second and third floors and were not shy about mentioning the difficulty it created for them. “If I had to do it over again, I’d probably use formaldehyde-free plywood instead,” Jeff says.On-Demand Not So Demanding
While American homes use water tanks that have to be continually heated, most European and Japanese homes use tankless hot-water heaters. Also called on-demand water heaters, these units conserve both space and energy, and their average life span is about 20 years—twice as long as conventional hot water heaters. The Feldmans chose a tankless system for their home to save energy in the long-term. Tankless systems are available in electric or gas-powered versions, and can be installed in any new or existing home. They come in a variety of sizes: large, which can heat enough water for two showers and a dishwasher running simultaneously, and small “one-fauceters” that can fit below a bathroom or kitchen sink. The Feldmans selected a large Takagi gas heater that’s about as big as a medium-sized backpack. “People always ask us, ‘Why don’t we have one of these?’” Jeff says, admitting that they cost about $1,200, compared to $600 for a traditional hot-water heater. “Our propane guy only comes out every six months because we use very little gas. So, it’s the difference between being far- and shortsighted.”Crops in the Kitchen
In lieu of solid wood or particleboard for the kitchen cabinet shelves and drawers, the Feldmans selected a material with a far greater “cool” factor—wheatboard, made from leftover straw during wheat processing. The cost of wheatboard falls somewhere between particleboard and solid wood, and it’s a much greener material, Jeff says. “We chose it for the look—the wheat grains are beautiful and still visible—and because we don’t have to worry about outgassing,” he says, explaining that wheat naturally binds to itself so there is no need for chemical adhesives. Staying with the green theme, he used a water-based finish on the shelves, and chose solid cherry wood for the drawer and door fronts. “I also love the feel of wheatboard, because you can actually feel the wheat grain,” he says.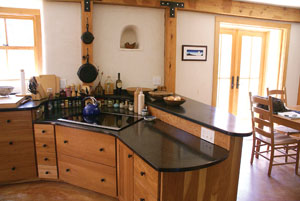
Newsy Counters
For kitchen counters, Jeff found an über-cool product from a company called shetkaSTONE. “The company makes countertops from any natural fibrous material—recycled newspaper, paper money, sunflower seeds and even jeans,” he says. Then they’re finished with water-based epoxy resin. The standard choices include counters made from shredded money for green countertops, newsprint for black, paper bags for brown and white paper for white. The more finely shredded the material, the purer the color. The Feldmans chose the sleek ebony color that comes from finely shredded recycled newsprint to contrast with their home’s light earth tones. Although shetkaSTONE has standardized countertop choices, they do accommodate custom orders. “They told me about one of their clients, an artist, who saved his junk mail for two years and then had them make a table from it, and an architectural firm that had them make a conference table from old blueprints,” Jeff says. The only caveat to shetkaSTONE is that the counters can scratch, Jeff says. “But all you have to do is lightly buff out the area with a very fine Scotch-Brite pad.”Milk Jug Decks
Another über-green thing in the Feldmans’ home is the polylumber deck, made from recycled milk jugs and other high-density plastics. Jeff says polylumber beats out traditional pressure-treated wood, which is typically impregnated with chemicals to minimize insect damage and weathering. He also prefers polylumber to composite decking materials such as Trex, which aren’t recyclable because they’re wood and plastic bonded together.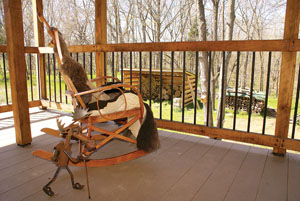