Green Guide: Growing “Green” Food
04 Jul 2010
The nation’s first net-zero greenhouse is being built and tested at a local organic farm by a Boulder firm, which hopes to develop it for residential applications so homeowners can grow vegetables year- round—without the associated astronomical energy costs.
It’s an odd disconnect: If you grow your own food, chances are you’re going to have to burn up a lot of fossil fuel. Anne Cure, proprietor of Cure Organic Farm in Boulder, knows this all too well. She’s tried the limited ways that are available to extend the growing season in her greenhouses, including filling 55-gallon drums with water so they’ll re-radiate daytime heat at night.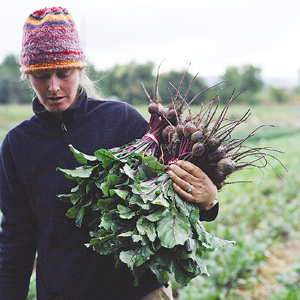
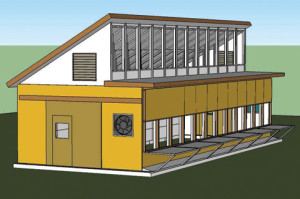
Pockets Full of Peppers
But between the parallel pieces of glass, there’s the shutter, a 2-inch piece of rigid insulation with a reflective coating. When the shutter is in its pocket, hidden in the top pane, you can look through the bottom pane—or the sun can shine through. Slide the shutter down, and the “window” becomes solid and reflective— perfect for deflecting the sun’s daytime rays, or for keeping warmth in at night. Once installed in the greenhouse, the pocket shutter motors will be controlled by electronics inside a box with light and heat sensors, with the option to switch to a manual setting. Other channels will open and close dampers so the greenhouse can cool down.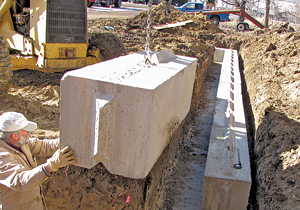
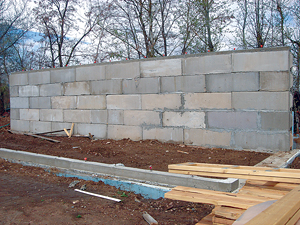